TWI Ltd, Granta Park, Great Abington, Cambridge CB21 6AL, UK
NAFEMS conference. July 2013.
Background
Welding thick walled components generates residual stresses which can be the cause of brittle fracture or corrosion cracking. Residual stresses can be reduced by heat treating which is applied to the whole component in a furnace. However, when the components are often too large to be furnace heat-treated, local heat treatment of a circumferential band (for a cylindrical geometry) or a circular patch (for a spherical cap) is allowed. This may be applied at circumferential butt welds or at branch or nozzle connections. British and American codes give recommendations regarding the size of the heat treated zone in order to avoid generating residual stresses due to the heat treatment whose magnitude may be larger than the residual stress in the weld after relaxation if applied incorrectly.
There is demand from industry to reduce the size of the heated zone, either to avoid overlapping other connections or heat sensitive attachments, or to reduce power consumption. However, a heated zone of reduced size will increase the thermal gradients and hence may generate unacceptable residual stresses during cooling. Finite element analysis (FEA) can be useful for optimising the procedure by predicting residual stresses whose magnitude may be compared to the acceptable value obtained from an ECA. In the present study, FEA was used to predict the residual stresses after local PWHT of a branch-pipe connection. Elastic and elastic-visco-plastic models were analysed assuming various heated zones geometries: constant width band, variable width band, circular patch or oval patch. Predicted residual stresses were compared with criteria from standards or the literature.
Dimension of the Heat-Treated Zones
British standards give recommendations on the size of the heated band (HB), where heating elements are applied, and the size of the gradient control band (GCB) which is covered with insulation pads. American standards address rather the size of the soak band (SB), where the heat treatment temperature must be kept within the specified interval. The table below summarises the sizes of SB, HB, and GCB for different standards:
|
Soak Band (SB)
|
Heated Band (HB)
|
Gradient Control Band (GCB)
|
BS2633
|
|
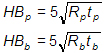 |
½ Tmax at the edge of HB
|
PD5500
|
|
 |
½ Tmax at the edge of HB
|
ASME B31.1
|
SB = 2t
|
|
Avoid harmful gradients.
|
ASME B31.8
|
SB = 102mm
|
|
T shall diminish gradually.
|
ASME I
|
SB = inf (2t, 102mm)
|
can be larger than SB to avoid harmful gradients
|
Avoid harmful gradients.
|
AWS D10.10
|
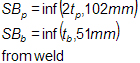 |
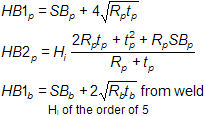
|
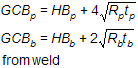 |
Where Rp and Rb are the radii of the pipe and the branch respectively, tp and tb are the wall thicknesses of the pipe and the branch respectively, and Tmax is the maximum heat treatment temperature
Methodology Applied for Modelling Local PWHT
The mid-thickness diameter of the modelled pipe was 360mm, and its wall thickness was 63mm. The mid-thickness diameter of the branch was 63mm and its wall thickness was 10mm. The pipe and branch were made of 0.5Cr-0.5Mo-0.25V steel.
For each model, the residual stress field was obtained in two steps: The temperature field at steady state was first obtained from a heat transfer analysis. Then the stress analysis was performed assuming the temperature increased linearly from room temperature to the steady state temperature field, was held for two hours so that stress relief can take place (in the case of the elastic-visco-plastic analyses) and was then decreased back to room temperature.
A range of different cases were simulated including circumferential bands 250mm or 510mm each side of the weld, triangular bands 300mm each side of the weld at the widest point, and 510mm (but with a soak band deliberately narrow but still within the ASME recommendation), circular or oval patches 300mm, 355mm, 410mm, or 465mm in radius. Figure 1 shows some of the temperature profiles obtained at steady state.
The thermal stress analyses were either elastic, assuming zero stress at PWHT temperature, or elastic-visco-plastic. In the latter case, the full heat treatment cycle was modelled, and an initial residual stress field from welding was assumed before heat-treatment. Elastic analyses were performed in order to compare the predicted stresses with those analytically obtained in the 1960s, and which were used to define the British standards (Burdekin, 1963, Cotterell, 1963).
Results
The results obtained show that the predicted residual stress values are of similar magnitude for the four patch sizes analysed. No significant difference was observed when comparing the results obtained with the 300mm circumferential and the 300mm triangular heated band. However analyses of the triangular soak band models show the influence of the soak band size. When the latter was deliberately reduced (but still within the recommendations of the American standards), high residual stress was predicted. In other cases, when defining the heated band size following British standards, the soak band was found to be systematically far larger than recommended by the ASME codes.
Figure 2 shows the largest residual stress values predicted from the analyses of four of the heated band geometries investigated. Apart from a peak stress at the weld toe, the residual stresses caused by the temperature gradient were in general predicted to be lower when the analyses were elastic-visco-plastic than when they were elastic only. This can be explained by the fact that the thermal stress at PWHT temperature is not zero, as assumed in the elastic-only models, but is partly defined by the temperature distribution during PWHT. The residual stresses at PWHT temperature whose level was below yielding is then relieved during the cooling step. The stress level was found to be lower or equal to the 30% of room temperature yield stress, as recommended by BS7910 (BS7910, 2005) for ECAs, or 50% of the room temperature yield stress as suggested by Cotterell (Cotterell, 1963), or 0.05αET0 as suggested by Burdekin, where T0 is the heat treatment temperature, α and E are the thermal expansion coefficient and Young’s modulus respectively. However, these findings do not apply to the case were the soak band was reduced to 75mm.
Main Conclusions
- Residual stresses predicted from an elastic analysis of the cooling stage are in general larger in magnitude than those predicted from an elastic-visco-plastic analysis of the full cooling cycle.
- A variable width heated band (triangular) allows residual stress to be reduced to a magnitude similar to that obtained after a local PWHT using a constant width circumferential band.
- Using circular or oval patches allows relaxation of the stress, but the residual stress predicted after cooling was about 20MPa to 50MPa higher than obtained from a band heat treatment.
- The soak band width must be significantly larger than the minimum width recommended by the ASME codes. This is the case when the heat treated band width is larger than the minimum allowed by the British codes (2.5√Rt each side of the weld).
- The results reported here were obtained from finite element models only. Experimental measurement of the residual stress after local post-well heat treatment of an identical joint geometry must be performed for validation.
References
- ASME I, Rules for Construction of Power Boilers, The American Society of Mechanical Engineers, 2001.
- ASME B31.1, Power Piping, The American Society of Mechanical Engineers”, 1998.
- ASME B31.8, Gas Transmission and Distribution Piping Systems, The American Society of Mechanical Engineers, 1999.
- AWS D10.10, Recommended Practices for Local Heating of Welds in Piping and Tubing, ANSI, 1999.
- BS2633, Specification for Class I Arc Welding of Ferritic Steel pipework for Carrying Fluids, Section one. 1987.
- BS7910, Guide on Methods for Assessing the Acceptability of Flaws in Metallic Structures, BSI Standards, 2005.
- Burdekin F M, Local Stress Relief of Circumferential Butt Welds in Cylinders, British welding Journal, pp 483,490, 1963.
- Cotterell B, Local Heat Treatment of Spherical Vessels, British Welding Journal, pp91-97, 1963.
- PD5500, Unfired Fusion Welded Pressure Vessels, BSI Standards, 2000
Additional information
More detailed results about this work can be found in TWI CRP Report No 13837.01/02/1162.02. A group sponsored project (GSP) proposal is currently under preparation for prediction and measurement of residual stresses after local PWHT in various joint geometries.
For more information, please contact us.