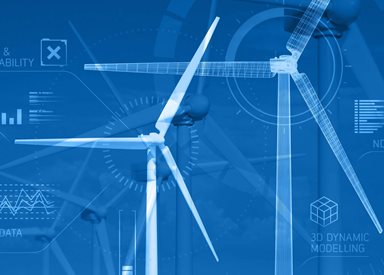
A digital twin is a digital representation of a physical object, process, service or environment that behaves and looks like its counterpart in the real-world.
A digital twin can be a digital replica of an object in the physical world, such as a jet engine or wind farms, or even larger items such as buildings or even whole cities, alternatively digital twin technology can be used to replicate processes in order to collect data to predict how they will perform.
A digital twin is, in essence, a computer program that uses real world data to create simulations that can predict how a product or process will perform. These programs can integrate the internet of things (Industry 4.0), artificial intelligence and software analytics to enhance the output.
With the advancement of machine learning and factors such as big data, these virtual models have become a staple in modern engineering to drive innovation and improve performance.
In short, creating one can allow the enhancement of strategic technology trends, prevent costly failures in physical objects and also, by using advanced analytical, monitoring and predictive capabilities, test processes and services.
If you have any questions or need help, email us to get expert advice:
contactus@twi.co.uk
Contents
Click the links below to skip down to the relevant content within our guide:
The life of a digital twin begins with experts in applied mathematics or data science researching the physics and operational data of a physical object or system in order to develop a mathematical model that simulates the original.
The developers who create digital twins ensure that the virtual computer model can receive feedback from sensors that gather data from the real world version. This lets the digital version mimic and simulate what is happening with the original version in real time, creating opportunities to gather insights into performance and any potential problems.
A digital twin can be as complex or as simple as you require, with differing amounts of data determining how precisely the model simulates the real world physical version.
The twin can be used with a prototype to offer feedback on the product as it is developed or can even act as a prototype in its own right to model what could occur with a physical version when built.
Since it can be used across a wide range of industries, from automotive to healthcare and power generation, it has already been used to solve a large number of challenges. These challenges include fatigue testing and corrosion resistance for offshore wind turbines and efficiency improvements in racing cars. Other applications have included the modelling of hospitals to determine work flows and staffing to find procedure improvements.
A digital twin allows users to investigate solutions for product lifecycle extension, manufacturing and process improvements, and product development and prototype testing. In such cases, a digital twin can virtually represent a problem so that a solution can be devised and tested in the program rather than in the real world.
The concept of digital twins was first put forward by David Gelernter’s 1991 book ‘Mirror Worlds,’ with Michael Grieves of the Florida Institute of Technology going on to apply the concept to manufacturing.
By 2002, Grieves had moved to the University of Michigan when he formally introduced the digital twin concept at a Society of Manufacturing Engineers conference in Troy, Michigan.
However, it was NASA who first embraced the digital twin concept and, in a 2010 Roadmap Report, John Vickers of NASA gave the concept its name. The idea was used to create digital simulations of space capsules and craft for testing.
The digital twin concept spread further still in 2017, when Gartner named it as one of the top 10 strategic technology trends. Since then, the concept has been used in an ever-growing array of industrial applications and processes.
Digital twin can be broken down into three broad types, which show the different times when the process can be used:
- Digital Twin Prototype (DTP) - This is undertaken before a physical product is created
- Digital Twin Instance (DTI) – This is done once a product is manufactured in order to run tests on different usage scenarios
- Digital Twin Aggregate (DTA) – This gathers DTI information to determine the capabilities of a product, run prognostics and test operating parameters
These over-arching types can offer a variety of uses including logistics planning, product development and re-design, quality control / management, and systems planning.
A digital twin can be used to save time and money whenever a product or process needs to be tested, whether in design, implementation, monitoring or improvement.
As mentioned above, digital twins can be created for a wide range of applications, for example, to test a prototype or design, assess how a product or process will work under different conditions, and determine and monitor lifecycles.
A digital twin design is made by gathering data and creating computational models to test it. This can include an interface between the digital model and an actual physical object to send and receive feedback and data in real time.
Data
A digital twin requires data about an object or process in order for a virtual model to be created that can represent the behaviours or states of the real world item or procedure. This data may relate to the lifecycle of a product and include design specifications, production processes or engineering information. It can also include production information including equipment, materials, parts, methods and quality control. Data can also be related to operation, such as real-time feedback, historical analysis and maintenance records. Other data used in digital twin design can include business data or end-of-life procedures.
Modelling
Once the data has been gathered it can be used to create computational analytical models to show operating effects, predict states such as fatigue, and determine behaviours. These models can prescribe actions based on engineering simulations, physics, chemistry, statistics, machine learning, artificial intelligence, business logic or objectives. These models can be displayed via 3D representations and augmented reality modelling in order to aid human understanding of the findings.
Linking
The findings from digital twins can be linked to create an overview, such as by taking the findings of equipment twins and putting them into a production line twin, which can then inform a factory-scale digital twin. By using linked digital twins in this way it is possible to enable smart industrial applications for real world operational developments and improvements.
The benefits of digital twin differs depending when and where it is used. For example, using digital twin to monitor existing products, such as a wind turbine or oil pipeline, can reduce maintenance burdens and save many millions in associated costs. Digital twins can also be used for prototyping ahead of manufacture, reducing product defects and shortening time to market. Other instances of digital twin use can include process improvements, whether that is monitoring of staffing levels against output or aligning a supply chain with manufacturing or maintenance requirements.
Common benefits include increased reliability and availability through monitoring and simulation to improve performance. They can also reduce risk of accidents and unplanned downtime through failure, lower maintenance costs through predicting failure before it occurs, and ensure production goals are not impacted by scheduling maintenance, repair and the ordering of replacement parts. Digital twin can also offer continued improvements by analysing customisation models and ensure product quality through performance testing in real time.
However, for all of the benefits, digital twin is not suitable in all instances as it can increase complexity. Some business problems simply do not need a digital twin and can be solved without the associated investment in time and cost.
Examples of digital twin can be found across industry and beyond for manufacturing, maintenance and failure prevention / lifecycle monitoring.
Applications range from automotive uses where telemetry sensors provide feedback from vehicles to the digital twin program, factories where processes are simulated by digital twin to provide improvements, and healthcare where sensors can inform a digital twin to monitor and predict the well-being of a patient.
Through the integration of technologies such as artificial intelligence, machine learning and software analytics with data, digital twin creates a simulation model that can update alongside or in lieu of a physical counterpart. This allows companies to assess an entirely computerised development cycle from design to deployment and even decommissioning.
By mimicking physical assets, frameworks and operations to produce continuous data, a digital twin allows industry to anticipate downtime, react to changing circumstances, test design improvements and much more.
Digital twin is key to the development of Industry 4.0 to provide automation, data exchange and joined-up manufacturing processes as well as de-risking product rollout. Industry employees are able to monitor operations in real time, providing prior alerts of possible failures and allowing for real time performance optimisation and assessment with minimal loss of productivity.
Digital twins are used in a wide variety of industries for a range of applications and purposes. Some notable examples include:
Manufacture
Digital twins can make manufacturing more productive and streamlined while reducing throughput times.
Automotive
One example of where digital twins are used in the automotive industry is to gather and analyse operational data from a vehicle in order to assess its status in real time and inform product improvements.
Retail
Outside of manufacture and industry, digital twin is used in the retail sector to model and augment the customer experience, whether at the level of a shopping centre or for individual stores.
Healthcare
The medical sector has benefitted from digital twin in areas such as organ donation, surgery training and de-risking of procedures. Systems have also modelled the flow of people through hospitals and track where infections may exist and who may be in danger through contact.
Disaster Management
Global climate change has had an impact across the world in recent years, yet digital twin can help to combat this by the informed creation of smarter infrastructures, emergency response plans and climate change monitoring.
Smart Cities
Digital twin can also be used to help cities become more economically, environmentally and socially sustainable. Virtual models can guide planning decisions and offer solutions to the many complex challenges faced by modern cities. For example, real time responses to problems can be informed by real time information from digital twins to allow assets such as hospitals to react to a crisis